by Rembrandt Elise
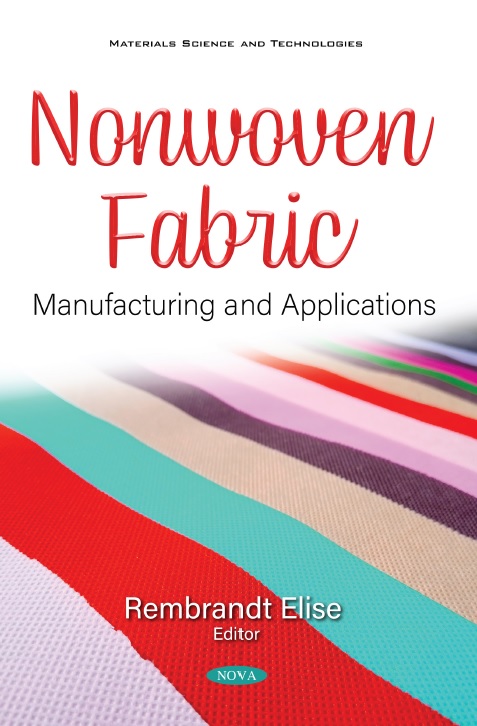
CONTENTS
Chapter 1 Natural Fibre Nonwovens 1
Subhankar Maity
Chapter 2 Potential of Jute Based Needle-Punched
Nonwoven: Properties and Applications 37
Surajit Sengupta
Chapter 3 Development of Needle Punched Nonwovens
for Thermal Insulation Applications 101
N. Muthukumar and G. Thilagavathi
Chapter 4 Development of Thermal Bonded Nonwoven
Fabrics Made from Reclaimed Fibers for
Sound Absorption Behaviour 121
S. Sakthivel, S. Senthil Kumar and
Seblework Mekonnen
Chapter 5 Boric Acid Based Fire-Retardants and
Nonwoven Fabric Surface Coatings for
Safety in the Automotive Industry 141
Nazan Avcioğlu Kalebek and Emel Çinçik
Chapter 6 Nonwoven Geotextiles in Civil
and Environmental Engineering 155
José Ricardo Carneiro, Filipe Almeida,
David Miranda Carlos
and Maria de Lurdes Lopes
Index 195
PREFACE
Nonwoven industry plays an important role in economy and society. Nonwoven Fabric: Manufacturing and Applications addresses important data on both natural and synthetic fibres that are used in the industry to develop products for different purposes.
Though synthetic fibres are extensively used in the nonwoven industry for the manufacture of various products, natural fibres are steadily occupying the market due to some of their obvious merits. In this respect, a review of the various manufacturing techniques for nonwoven fabric derived from natural fibres such as cotton, jute, flax and hemp is given in this book.
Next, the authors assess the structure, property, evaluation and applications of jute and jute blended needle-punched nonwoven fabric, in an effort to aid those who work with natural lingo-cellulosic fibre-based needle punched nonwovens.
In addition, flax/low melting point polyester needle punched nonwoven fabrics were manufactured and characterized for thermal insulation applications. The test results show a decrease in thermal resistance value with an increase in low melt PET % and needle penetration depth.
Six types of recycled nonwovens samples were developed using thermal bonding and aero dynamic methods, and these samples are characterized by their physical properties such as areal density, bulk density, thickness, porosity, air permeability and thermal resistance.
The authors assess the way in which the increased use of fire retardant materials in industries has put considerable pressure on the scientific community to develop new polymer materials, chemicals, and fiber combinations for such applications.
This compilation concludes with an overview of the history, common raw materials, manufacturing processes, properties, functions and applications of nonwoven geotextiles. The potential use of recycled nonwoven geotextiles towards a more sustainable construction is also discussed.
Chapter 1 – Though synthetic fibres are extensively used in nonwoven industry for manufacturing various products, natural fibres are steadily gearing up occupying the market due to some of their obvious merits. This paper reviews various manufacturing techniques of nonwoven fabric from natural fibres such as cotton, jute, flax, hemp etc. It has been observed that carding, air-laying, and wet-laid techniques could be used for web formation, and needlepunching, hydroentangling, stitch bonding, and thermal bonding could be used for web bonding of the natural fibres.
Carding and needlepunching process has been mostly used for manufacturing of the natural fibre nonwovens. A huge scope of potential applications of these nonwovens in various field of geotextiles, filtration, automotive, upholstery, acoustic insulation, thermal insulation etc. have been discussed here.
Chapter 2 – Uses of nonwoven fabric in domestic and industrial areas are increasing day by day. Now-a days, research is going on to apply natural fibre in different uses in the form of nonwoven either alone or blended with synthetic fibres. The chapter presents with an idea regarding the structure, property, evaluation and application of jute and jute blended needle-punched nonwoven fabric. Knowing well about the effect of various factors on the needle-punched jute nonwoven, the proper and effective design can be made of such fabrics for a particular use. This chapter is intended to present an overview and potential — most of which are based on ideas and conclusions presented in published literature during the last 40 years, the rest representing the author’s concepts developed through extensive research. It will help to those who will deal with natural lingo-cellulosic fibre-based needle punched nonwoven in both industry and academia especially to teachers, students and technologists.
Chapter 3 – Today the nonwoven technology, is considered as the most modern method, constitutes for the low cost substitutes for producing textiles. Among textile applications, nonwovens, one of the fastest growing sector constitutes about one-third of the fiber industry. Nonwoven materials are porous materials consisting of fibres and interconnected voids. Due to their unique fibre orientation and porous structure, nonwovens are ideal materials for insulation applications. Needle punching is one of the simplest and oldest methods of nonwoven fabrication. In this work, flax/low melting point polyester needle punched nonwoven fabrics were manufactured and characterized for thermal insulation applications.
Nonwovens were developed by blending flax fibers with low melt PET at 3 blend ratios (10%, 20% & 30%) with 7mm & 10 mm needle penetration depth. The influence of blend ratio and needle penetration depth on the performance of the nonwovens was studied. The test results showed that there was a decrease in thermal resistance value with increase in low melt PET % and needle penetration depth. Also the performance of the developed nonwovens compared with commercial product.
Chapter 4 – Recycled fibers are commonly used in different applications, sound absorption being one of the most important applications. Recycled fiber nonwovens are currently high in demand in industries because of their advantages such as low cost, biodegradability, acceptable mechanical and physical properties and so on. Sound absorption materials such as renewable and eco-friendly thermal bonded nonwoven have been developed using recycled cotton and polyester fibers. Six types of recycled nonwovens samples were developed using thermal bonding and aero dynamic methods. The blending ratio of cotton and polyester fibers was 60:40. Sound absorption coefficient was measured by impedance tube method (ASTM E 1050). The recycled fiber nonwoven samples are characterized by their physical properties such as areal density, bulk density, thickness, porosity, air permeability and thermal resistance was determined for all the samples according to the ASTM standards. The results exposed that recycled cotton/polyester nonwoven samples with its physical properties showed superior sound absorption at 4000 Hz, lower thermal resistance, lower air permeability. Then compared with recycled cotton/polyester are corresponding to the achieved level but it was lower in recycled cotton/polyester nonwoven samples. But, at superior frequencies (4000 Hz), there was a decrease from the achieved level in all the nonwoven samples which might be enhanced by increasing the thickness of the nonwovens. The average sound resistance percentages of these three decibel values were calculated and compared for all the samples.
Chapter 5 – Nonwoven fabrics are porous webs which are produced directly from fibers. Not only natural fibers but also man-made fibers are used in web production and bonding. Nonwoven fabrics continue to be one of the fastest growing material types being used in the textile industry.
They are considered to be engineered fabrics with excellent performance properties. Over the past two decades, increasing uses are being found for nonwoven fabrics in many fields due to the ease of the manufacturing process, high production speeds, and lower production costs. Nonwovens are used almost everywhere including in the military, agriculture, construction, clothing, home furnishings, travel and leisure, healthcare, personal care and for household applications. These fabrics demonstrate much functionality such as strength, resilience, absorbency, liquid repellency, softness and etc. One primary functionality is as a flame retardant. Flame retardants are important for personal safety and for reducing losses caused by fire. Most recently established federal regulations on the flammability of the fabric indicate that the use of FR textiles will steadily increase in the near future. The increasing use of FR materials in industry has put considerable pressure on the scientific community to develop new polymer materials, FR chemicals, and fiber combinations to a wide range of end use applications. Boric acid has recently been used in textile materials as a flame retardant. Boric acid (commercially known as Optibor®) is a white triclinic crystal in water (5.46 wt.%), alcohols, and glycerin. It has the chemical formula H3BO3 (sometimes written B(OH)3), and exists in the form of colorless crystals or a white powder that dissolves in water. Boric acid is found naturally in its free state in some volcanic regions. Flame retardant chemicals only minimize fire risk however they are not completely non-flammable. With flame retardancy, people have time to escape, ignition times are reduced and the release of toxic gases is minimized. In this study, polyester (PES) based nonwoven fabrics produced by air layering and spunlace techniques were used as samples. They have been used for interior car roofs and interior door linings. Boric acid (BA) was applied to nonwoven fabrics as a finishing operation by spraying and brushing at the completion of the spunlace production systems. The applied amount of 2.58 g boric acid was mixed with 250 ml of warm water at 32ºC based on the chemical properties as written in the information chart for the chemicals. The flammability test was evaluated according to the ASTM D2863 standard under controlled conditions. The Limiting Oxygen Index (LOI) is a test method for evaluating the ignition and ease of flame extinction in samples. Fabrics having an LOI value of 21 or below ignite easily and burn rapidly in air.
LOI values above 21 ignite and burn more slowly. When LOI values are above 26-28, the fabric may be considered to be flame retardant. As a result, the LOI value of untreated PES nonwoven fabrics were measured at 16.2 for 45 g/m2. The LOI value of PES fabrics treated with the solution increased to 26.8 for 200 g/m2. This result confirms that the boric acid had a great influence on the flammability resistance of nonwoven fabrics.