By Subramanian Senthilkannan Muthu
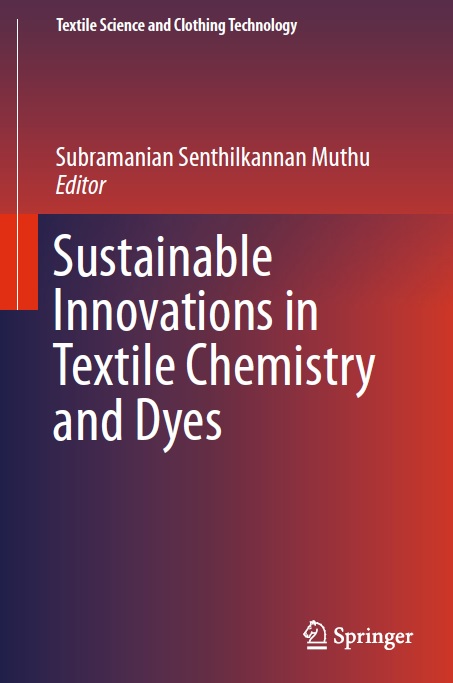
Contents
M. Gopalakrishnan, K. Shabaridharan and D. Saravanan
2 A Review of Some Sustainable Methods in Wool Dyeing . . . . . . . . . 21
N. Gokarneshan
3 Green Chemistry in Textiles . . . . . . . . . . . . . . . . . . . . . . . . . . . . . . . 53
P. Senthil Kumar and E. Gunasundari
4 Bioremediation: Green and Sustainable Technology
for Textile Effluent Treatment . . . . . . . . . . . . . . . . . . . . . . . . . . . . . 75
Luqman Jameel Rather, Sabiyah Akhter and Qazi Parvaiz Hassan
Low Impact Reactive Dyeing Methods for Cotton for Sustainable Manufacturing
Abstract
The reactive dyes, though result in higher fastness properties compared to other classes of dyes used in colouration of cotton fibres, lead to problems related to effluents predominantly due to unreacted and hydrolysed dyes during the reaction.
Besides, use of higher amounts of salts added during the exhaustion (30–70 g/L) and fixation process (10–20 g/L) also result in higher COD levels in the effluents. Suitable modifications of dyes to improve the reactivity or to lower the hydrolysis and modification of substrates to have more reactive sites could provide a sustainable solution to such problems. Various scopes available for modifying the substrates suitable for reactive dye applications and different structural modifications carried out in the reactive dyes to reduce the environmental impacts are discussed in this chapter.
Introduction
The Global Fiber Consumption Survey 2016 conducted by the Lenzing reinstates the dominant position of cotton fibres, with the consumption of cotton fibre for apparels around 25% [1]. Majority of the apparels are still produced with cotton fibre for its softness and breathability. On the other hand, majority of cotton materials are dyed with reactive dyes for all-round fastness properties. Reactive dyes are preferred in the case of cotton wherever the chlorine fastness is not demanded, significantly. Prior to the commercial applications of reactive dyes in the year 1956, cotton substances were dyed with direct dyes and, vat and acid dyes with certain pre-treatments. Substantivity of dyes eliminates the pretreatments and simplifies the dyeing process. Needless to state, the substantive reactive dyes satisfy the customer needs that the dyed substances would withstand severe washing and service conditions. Reactive dye is the one that forms a strong covalent bond with the side chain of cellulose that leads to good fastness properties. Reactive dyes are also recommended for their brilliancy and it’s varieties in colour [2, 3].
Structure of the reactive dyes makes them more attractive, by covalently reacting with the substrates, which also leads to less impact onto the environment with reasonably better fastness properties. The characteristic features of a typical reactive dye molecule include, (i) chromophoric grouping, contributing the colour and much of the substantivity for cellulose; (ii) reactive system, enabling the dye to react with the hydroxyl groups in cellulose; (iii) bridging group that links the reactive system to the chromophore; and, (iv) one or more solubilising groups, usually sulphonic acid substituents attached to the chromophoric group. In general, reactive dyes react with hydroxyl groups present in cellulose and form covalent bond with cellulose under alkaline conditions that has been extensively dealt in the past. Mostly, one cellulosic molecule is attached to one reactive site in the reactive dye. However, sometimes two cellulosic molecules may attach to two reactive groups in dyes. Reactive dyes also react with hydroxyl groups present in water, leading to hydrolysis of the dyes and loss of dyes. These dead dyes cannot react with cellulose further and cause increase in the effluent loads. These hydrolyzed dyes not only leads to poor colour yield, this may also leads to poor fastness and needs severe washing and soaping treatments to remove the unfixed dyes. Reactive dyes are more substantive towards cellulose rather than water molecule, so 60–70% of the reactive dyes are exhausted on cotton fibres, in the original form, and 30–40% of dyes may react with water and leads to lower colour yield [4].
However, suitable modifications of the reactive dye structure further and surface of the reacting surface (fibres and fabrics) are often explored to improve the reactivity between fibres and dyes, thereby reducing the environmental impacts. Table 1 shows the various possibilities to improve the reactivity and reduce the amount of un-reacted dyes let into the effluents.