Introduction
In the packaging industry, ensuring the durability and strength of materials is crucial to protecting products during storage and transportation. One of the most widely used testing methods for assessing the strength of packaging materials, especially corrugated boxes, is the bursting strength test. This test is conducted using a bursting strength machine, an essential instrument in quality control for packaging manufacturers, suppliers, and third-party testing laboratories.
In this article, we will explore the principles of the bursting strength machine, its working mechanism, and its significance in evaluating the burst strength of corrugated boxes.
What Is a Bursting Strength Machine?
A bursting strength machine is a specialized testing instrument used to measure the resistance of paper, cardboard, textiles, and other materials to rupture under pressure. This test is essential for evaluating the durability and structural integrity of packaging materials.
The machine applies hydraulic or pneumatic pressure on a sample until it bursts, and the pressure at the point of rupture is recorded in pounds per square inch (psi) or kilopascals (kPa). The higher the bursting strength, the more resistant the material is to external pressure and impact forces.
Key Components of a Bursting Strength Machine
- Rubber Diaphragm – Expands to apply uniform pressure to the sample.
- Hydraulic/Pneumatic System – Controls the pressure application.
- Clamp System – Holds the sample firmly in place.
- Pressure Gauge or Digital Display – Records the burst strength reading.
- Control Panel – Allows users to set parameters and monitor the test process.
Types of Bursting Strength Machines
- Analog Bursting Strength Tester – Uses a manual gauge to display results.
- Digital Bursting Strength Tester – Provides precise readings and may include data logging capabilities.
- Microprocessor-Based Bursting Strength Tester – Offers advanced features such as automatic calibration, data storage, and connectivity options.
How Does a Bursting Strength Machine Work?
The operation of a bursting strength machine follows a standardized testing procedure:
- Sample Preparation – A piece of the test material (e.g., corrugated board, paper, fabric) is cut to the required dimensions.
- Mounting the Sample – The sample is clamped securely between the upper and lower fixtures of the machine.
- Application of Pressure – The rubber diaphragm expands as hydraulic or pneumatic pressure is applied uniformly across the sample’s surface.
- Bursting Point Measurement – The pressure at which the sample ruptures is recorded.
- Result Interpretation – The bursting strength value is analyzed to determine the material’s quality and performance.
Importance of Bursting Strength in Packaging Industry
The burst strength of corrugated boxes and other packaging materials directly impacts product protection, transportation efficiency, and overall customer satisfaction. Here’s why it matters:
1. Ensuring Packaging Durability
Corrugated boxes are widely used for shipping and storage. The bursting strength test helps manufacturers verify whether a box can withstand external forces without breaking, reducing the risk of product damage.
2. Compliance with Industry Standards
Regulatory bodies such as ASTM (American Society for Testing and Materials), ISO (International Organization for Standardization), and TAPPI (Technical Association of the Pulp and Paper Industry) establish guidelines for packaging quality. Testing with a bursting strength machine ensures compliance with these standards.
3. Reducing Material Waste
By accurately assessing the strength of materials, manufacturers can optimize their material selection and reduce excess use of raw materials, leading to cost savings and environmental benefits.
4. Enhancing Customer Satisfaction
Strong packaging reduces the chances of damaged goods, leading to higher customer satisfaction and lower return rates.
Burst Strength vs. Edge Crush Test (ECT): Which One Should You Use?
In corrugated packaging, two primary strength tests are commonly used: the burst strength test and the edge crush test (ECT).
- Burst Strength Test (using a bursting strength machine) measures the material’s resistance to internal and external forces applied over a broad area. It is suitable for evaluating overall package durability.
- Edge Crush Test (ECT) assesses the stacking strength of a box by measuring its resistance to crushing when compressed vertically. It is ideal for determining how well a box can support heavy loads during storage.
Which One to Choose?
Use burst strength testing if your priority is resistance to punctures, impact, and external pressure.
Use ECT testing if your concern is vertical stacking strength and warehouse storage efficiency.
Factors Affecting Bursting Strength of Corrugated Boxes
Several factors influence the burst strength of corrugated boxes, including:
- Paper Quality – The grade and thickness of the kraft paper used in corrugated boards affect burst resistance.
- Flute Type – Different flute sizes (A, B, C, E, F) influence a box’s structural integrity.
- Adhesive Quality – The strength of the adhesive bonding the layers impacts overall durability.
- Moisture Content – Excessive moisture weakens the material, reducing burst resistance.
- Manufacturing Process – Variations in production techniques can lead to inconsistencies in box strength.
Choosing the Right Bursting Strength Machine for Your Needs
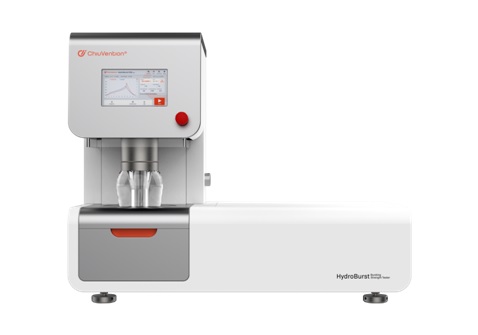
When selecting a bursting strength machine, consider the following factors:
- Accuracy and Precision – Ensure the tester provides reliable and repeatable results.
- Compliance with Standards – Choose a machine that meets ASTM D3786, ISO 2759, or TAPPI T810 standards.
- Automation Features – Digital and microprocessor-based models offer better data handling and user-friendliness.
- Testing Range – Check the pressure range of the machine to match your material specifications.
Conclusion
The bursting strength machine is a crucial tool for testing the durability of packaging materials, especially in evaluating the burst strength of corrugated boxes. By ensuring that packaging meets industry standards and withstands transportation stresses, manufacturers can reduce product damage, improve customer satisfaction, and optimize material usage.
For businesses in the packaging and logistics industry, investing in a high-quality bursting strength tester is a step toward achieving better quality control and more reliable product protection.